Welcome to DOSAPEDIA
Here you can find detailed information on products and use cases as well as tips and tricks relating to the field of water treatment and disinfection.
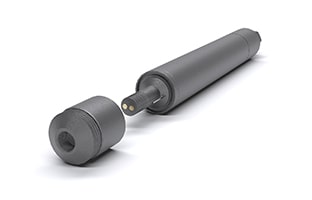
Three-electrode system
A 6 mm diameter nozzle in the flow cell at a distance of approximately 15 mm will provide a constant jet of disinfectant fluid (shown in the illustration by a blue arrow) perpendicular to the membrane surface (1).
Primarily, the membrane will only allow molecules of the disinfectant to pass through it. These molecules travel through the liquid electrolyte (2) to the working electrode (3). The working electrode (3) is made of precious metal (gold or platinum) to prevent it corroding. The working electrode (3) is subject to a very low, precisely controlled potential difference. As a result, the disinfectant releases electrons towards the surface of the working electrode. In a three-electrode system, the electrons flow to the return electrode (5) where they generate a very low electric operating current. The return electrode (5) is a stainless steel ring. This configuration ensures the reference electrode (4) is kept current-free. The operating current is measured and combined with the temperature to produce an electric signal (6). This signal may be a standard voltage signal from 0 to -2000 mV, a standard current signal from 4 to 20 mA or a standard bus signal for a ModBus RTU system.
The reference electrode (4) is coated with a very fine layer of silver chloride. In conjunction with each other, the coating and the electrolyte generate an extremely accurate zero-point voltage. It is only this exact zero point that enables the precise potential difference to be set for the surface of the working electrode.
Besides the signal connection (6) a supply voltage (7) is also required, depending on the type of output signal.
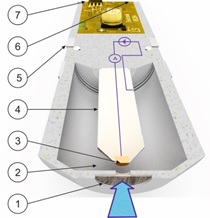
Two-electrode system
A 6 mm diameter nozzle in the flow cell at a distance of approximately 15 mm will provide a constant jet of disinfectant fluid (shown in the illustration by a blue arrow) perpendicular to the membrane surface (1).
Primarily, the membrane will only allow molecules of the disinfectant to pass through it. These molecules travel through the liquid electrolyte (2) to the working electrode (3). The working electrode (3) is made of a precious metal (gold or platinum) to prevent it corroding and is subject to a very low, precisely controlled potential difference. As a result, the disinfectant releases electrons towards the surface of the working electrode. The electrons flow to the reference electrode (4) where they generate a very low electric operating current. This operating current is measured and combined with the temperature to produce an electric signal (6). This signal may be a standard voltage signal from 0 to -2000 mV, a standard current signal from 4 to 20 mA or a standard bus signal for a ModBus RTU system.
The reference electrode (4) is coated with a very fine layer of silver chloride. In conjunction with each other, the coating and the electrolyte generate an extremely accurate zero-point voltage. It is only this exact zero point that enables the precise potential difference to be set for the surface of the electrode.
Besides the signal connection (6) a supply voltage (7) is also required, depending on the type of output signal.
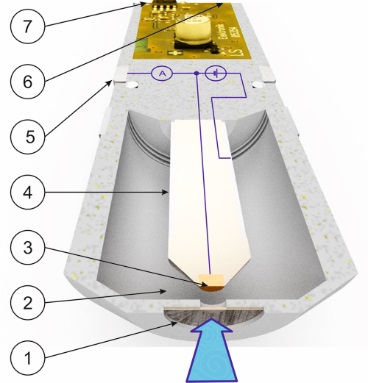
3-Elektroden-System
Eine Düse der Durchflussarmatur mit 6mm Durchmesser in etwa 15 Millimeter Entfernung bringt einen konstanten Strahl der Flüssigkeit (im Bild links symbolisiert durch blauen Pfeil) mit dem Desinfektionsmittel in senkrechter Richtung auf die Membran (1).
Die Membran lässt vorwiegend Moleküle des Desinfektionsmittels passieren. Diese Moleküle legen einen Weg in der Elektrolyt-Flüssigkeit (2) bis zur Arbeitselektrode (3) zurück. Die Arbeitselektrode (3) ist aus einem Edelmetall (Gold oder Platin) damit sie nicht korrodiert. Die Arbeitselektrode (3) steht unter einer sehr kleinen aber genauen elektrischen Spannung. Deshalb gibt das Desinfektionsmittel an der Oberfläche der Arbeitselektrode Elektronen ab. Diese Elektronen fließen im 3-Elektroden-System zur Gegenelektrode (5) und bilden einen sehr kleinen elektrischen Arbeitsstrom. Die Gegen-Elektrode (5) ist als Ring aus Edelstahl erkennbar. Durch diese Methode wird die Referenzelektrode (4) stromfrei gehalten. Der elektrische Arbeitsstrom wird gemessen und mit der Temperatur zu einem elektrischen Signal (6) verarbeitet. Dieses Signal kann ein Standard-Spannungs-Signal von 0 bis -2000 Millivolt oder ein Standard-Strom-Signal 4 bis 20 Milliampere oder eine Standard-Bus-Signal „ModBus RTU“ sein.
Die Referenzelektrode (4) besitzt eine sehr dünne Silber-Salz-Beschichtung. Gemeinsam bilden diese Beschichtung und der Elektrolyt einen sehr genauen Spannungs-Nullpunkt. Nur dieser genaue Nullpunkt ermöglicht, die exakte elektrische Spannung für die Oberfläche der Arbeits-Elektrode einzustellen.
Neben dem Signal-Anschluss (6) ist - abhängig vom Typ des Ausgangssignales - eine Spannungsversorgung (7) erforderlich.
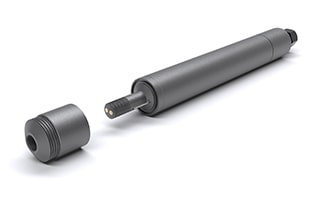
Membrane-free amperometric sensors
Primarily, the membrane will only allow molecules of the intended disinfectant to pass through it. This kind of selection is not possible without a membrane. In systems without a membrane, it is also not possible for the electrolyte to deliver some of its functionality, to buffer the pH or to distinguish between individual disinfectants. What is more, the all-important working electrode is subject to contamination from the soiling in the water, which makes it necessary to implement cleaning mechanisms or clean it using electric circuits.
Sensors without membranes are also less susceptible to changes in pressure. Sensors of the DOSASens AS family do not require any specially adapted electronic circuitry in the signal transmitter
.
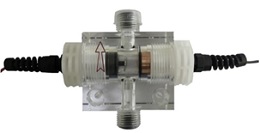
Copper-platinum sensors
The benefits of the membrane and electrolyte are not provided by copper-platinum sensors, because they have neither. Measurement of a disinfectant using the amperometric principle requires a precise potential difference between the reference electrode and the working electrode. In membrane-covered sensors, this potential difference is provided by the electronic circuitry itself and is set to an exact value.
By contrast, the copper-platinum sensor uses the natural voltage difference between the two metals copper and platinum. However, this natural potential difference is also dependent on the size of the surfaces, the water flow rate and the degree of oxidation. In standard systems of this kind, the copper surface is kept free of oxide by means of glass beads.
All in all, this system generates a potential difference that cannot be allocated unambiguously to a specific disinfectant. The electric currents flowing between the copper and platinum are, as a result, very low and require sophisticated processing. A copper-platinum sensor cannot be used without a special-purpose transmitter.
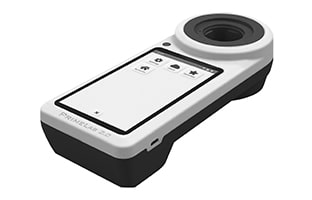
DPD photometer measurement
This method makes use of manual measurement by means of a photometer or a visual colour comparison, where continuous measurements are also an option. However, this method does not distinguish between different disinfectants because the system only measures or compares the same colour each time. In addition, due to the fact that the method is a manual one, considerable individual errors can occur – the result depends to some extent on the person conducting the measurement. Despite that, the procedure is needed as a comparison for the purpose of calibrating the transmitter.
DPD measurement is a patented process that is based on measuring the effect of the disinfectant on a dye. The dye is called dipropyl-p-phenylenediamine. The DPD process is adjusted to the intended disinfectant by means of conversion factors and supplemental substances.
How to find the right sensor...
The measured variables
Which disinfectant do we want to measure?
As a rule, it is not sufficient just to have a look at the container under the dosing pump. It is essential to understand the way the process works, because the disinfectant that has been added to the water may not actually be detectable in the water.
Example 1: Free chlorine has been added to a liquid manure used in agriculture – in this case, no free chlorine will be detected. The organic components, such as ammonium, will have converted free chlorine into bound chlorine. You will have to select the total chlorine subgroup.
Example 2: If free chlorine is added to seawater with a normal bromide content, the free chlorine will displace the bromine from the compounds. In this case, select the bromine option.
Example 3: Ozone is a more powerful oxidizing agent than free chlorine, which is why it will have the same effect on seawater as free chlorine. In this case, select the bromine option. Additionally, it helps to know that the DPD method can also produce false positives for seawater.
We will be pleased to assist you at any time in selecting the right sensor for your application.
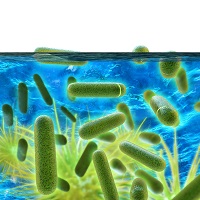
Legionella
Every pipe contains a biofilm colonised by legionella bacteria. Legionella are highly resistant bacteria, approx. 1 µm big, that multiply particularly effectively in warm water. They thrive in slightly larger amoebae, where they also reproduce. The bacteria are transmitted to humans by the inhalation of contaminated aerosols and are a serious risk to older people and those with weakened immune systems.
If contaminated water, in the form of water vapour, or aerosol, reaches the air, the legionella can find their way through the respiratory tract in the body and trigger legionnaires' disease. Legionnaires' disease has been known since 1976. At an American Legion convention in Philadelphia, 221 attendees caught the disease and 34 of them died. This is why it was given the name "legionnaires' disease". After that outbreak, intensive research was carried out and the cause was found to be the legionella bacterium.
In accordance with German standards (Drinking Water Act, Sec. 14(3)), the population of legionella in water supply systems must be monitored. If the limit value of 100 CFU per 100 ml is exceeded, the operators of the system are required to initiate technical countermeasures.